MONDAY @ AUTOMATE: Live Demo of 3Laws Dynamic Safety & AI Guardrails
Schedule
Mon May 12 2025 at 02:30 pm to 05:30 pm
UTC-04:00Location
Huntington Place | Detroit, MI
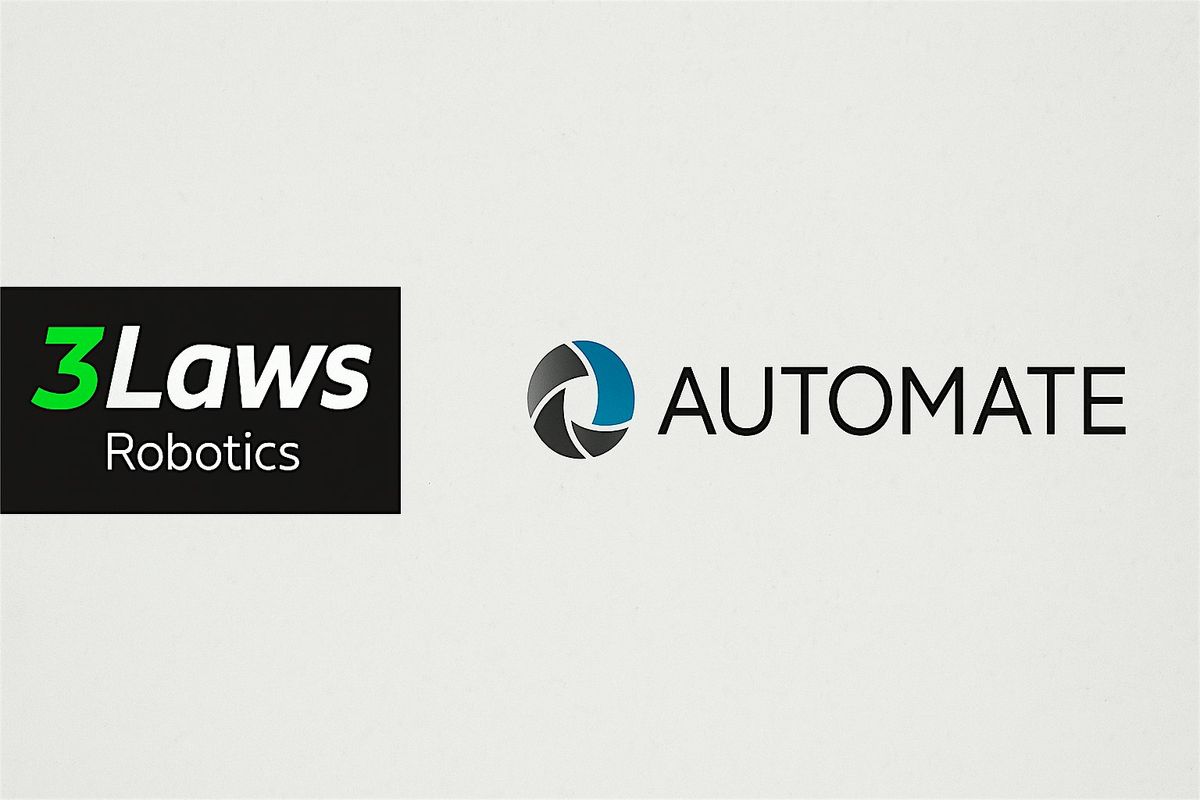
About this Event
AUTOMATE: Live Demo of 3Laws Dynamic Safety & AI Guardrails
Come join us at AUTOMATE 2025 for an exciting in-person event showcasing the latest in dynamic safety technology! Witness a live demo of our cutting-edge 3Laws system, complete with AI guardrails to keep your workplace safe and efficient. Don't miss out on this opportunity to see the future of safety in action - Booth 8922
As a refresher - Fulfillment & Logistics companies are using 3Laws to reduce time per mission and increase mean time between stop incidents.
- US Air Force: Flight-tested 3Laws' guardrails in the X62 Vista (F-16 Platform) for AI pilot safety, including geofencing and flight floor testing.
- Rover Robotics: Integrated 3Laws Supervisor to enhance reliability, boosting performance and simplifying navigation.
- Friendly Robot Company: Uses 3Laws for collision avoidance in vacuum cleaning robots, enabling close-to-wall operations.
- BP, Raytheon, Dow Chemical, Ford: Co-developed the technology with applications across business units.
Video:
Key Features and Use Cases
- Collision avoidance through real-time corrective actions, allowing robots to handle unexpected obstacles without replanning.
- Geofencing to keep robots within safe areas or away from restricted zones.
- System stability to ensure robots operate within defined safety and performance parameters.
- Human-robot interaction that supports safe, continuous operation near people.
- Fault mitigation for graceful performance degradation in case of sensor or hardware failures.
Customer Challenges Addressed
- Difficulty navigating close to obstacles.
- Slow or stalled navigation in dynamic environments.
- Overly conservative emergency-stop triggers.
- Excessive reliance on redundant sensors for safety.
- Complexity when deploying robots in new or rapidly changing environments.
For the rest of your team -- please share that the USAF recently tested our software with x62 Vista's AI pilots for collision avoidance and geofencing. We apply guardrails to anything that moves. Our dynamic safety layer is built exclusively for autonomous environments.
Collision Avoidance
Adjust motion commands in real-time to prevent accidents and damage when robots detect obstacles.
Geofencing
Restrict robot movement to designated areas, enhancing safety by preventing entry into hazardous zones.
Instability Safeguarding
Monitor robot balance to prevent tipping or falling in unstable conditions.
Fault Management
Automatically detect and respond to system errors, minimizing downtime and operational risks.
The other problem we are seeing more of is swarming management, occurring in same-system environments (e.g. multiple robots in a crowded or restricted space. At a minimum this leads to occasional manual/human intervention and can lead to productivity losses greater than twenty percent.
About 3Laws Robotics Pilot Program
Phase One: Compare the 3Laws Approach to Safety with a Ground Truth Approach
- Requirements Alignment: A joint meeting with our team to align on performance and safety requirements, creating a test plan to assess the next steps.
- Safety System and Sensor Modeling: Modeling of your safety system and its constraints, including sensor modeling to address how false positives are handled.
- Case Study: Running the 3Laws Supervisor on your system to explore opportunities to reduce safety violations and identify most valuable areas for impact.
- Review Case Study: Quantifying the incremental benefit of using 3Laws for dynamic safety.
- Decision Point: Based on results, determining whether to extend 3Laws to a more dynamic system.
Certifications and Standards
- General Support for Safety Certification: 3Laws helps companies make the safety case for robotic systems by providing evidence of system robustness, easing the certification path with our Supervisor Pro tier.
- ISO 26262 (Road vehicles – Functional safety): 3Laws uses Control Barrier Functions (CBFs) to enforce mathematically rigorous safety constraints, providing a deterministic safety layer between the autonomy stack and low-level controls to support functional safety and hazard mitigation.
- ISO 13849 (Safety of machinery — Safety-related parts of control systems): 3Laws' Supervisor Pro supports safety-rated control system design by working with existing sensors to prevent dangerous situations and gracefully degrading performance in case of sensor failure.
- ISO 10218 (Robots and robotic devices — Safety requirements for industrial robots): 3Laws enhances compliance by enforcing real-time collision avoidance, geofencing, velocity limits, and stability requirements to ensure safe robot operation in dynamic environments.
- ANSI B56.1 (Safety Standard for Low Lift and High Lift Trucks): 3Laws provides dynamic safety guardrails for forklifts, enabling obstacle and worker avoidance, safer material handling, and optional audio alerts for non-drive-by-wire forklifts.
- OSHA 3691 (Powered Industrial Trucks (Forklifts)): 3Laws helps employers maintain safe forklift operations by reducing accidents, preventing gridlocks, enabling safer human-robot interactions, and dynamically restricting access to hazardous areas.
Resources - Use Cases
- Video - Navigating the Challenges of High-Velocity Systems
- Video - Dynamic Safety Assurance of Autonomous Systems
- PPT - Dynamic Safety Guardrails for Industrial Robotics
- PPT - Dyanmic Safety Guardrails for Forklifts and AMRs
Where is it happening?
Huntington Place, Booth 8922, Detroit, United StatesEvent Location & Nearby Stays:
USD 0.00